Silage Livestock Feeds Production: Silage is fermented, high-moisture stored fodder.
Which can be fed to cattle, sheep and other such ruminants (cud-chewing animals).
Or used as a biofuel feedstock for anaerobic digesters.
It is fermented and stored in a process called ensilage, ensiling or silaging.
And is usually made from grass crops, including maize, sorghum or other cereals.
Using the entire green plant (not just the grain).
Silage can be made from many field crops.
Join us in our mission
For over a decade, we’ve been on a mission: to help everyone in the world learn how to do anything. Today, we’re asking that you join us. You can request publication of your article for publication by sending it to us via our Email
And special terms may be used depending on type: oatlage for oats, haylage for alfalfa.
Silage underneath plastic sheeting is held down by scrap tires.
Concrete beneath the silage prevents fermented juice from leaching out
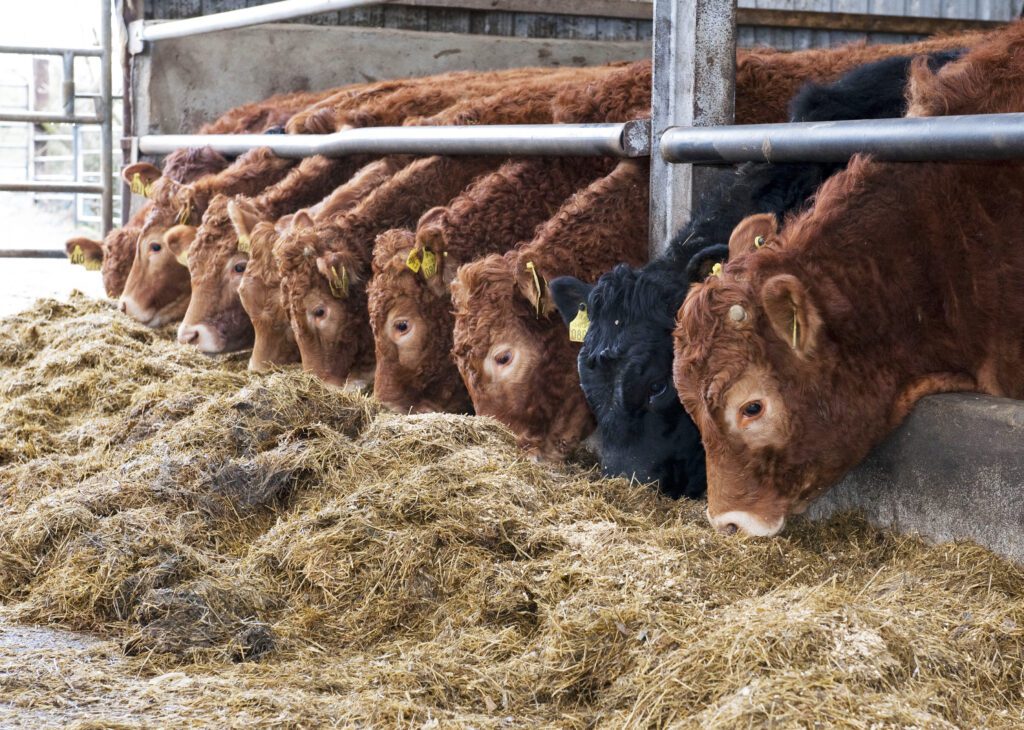
Silage Livestock Feeds Production:
1.Plan ahead.
- Timing is important for not only when the forage crop needs to be cut.
- But also to chop it up while the weather is good, have someone packing the pit as more fresh silage is collected, and to cover it up as soon as possible to allow it to ferment.
- If you have not yet found a site for and installed a concrete bunker, or dug into the ground an open three-sided pit designed for storing silage.
- You will need to have this arranged and completed well in advance of silage-making season.
- Or, if you do not have a bunker or pit dug out and prepared for proper ensiling.
- You need to find a place where you can create a silage pile that is well-drained and easily accessible during times when you need to access it without much trouble.
- When making silage, it’s doubly important to have the correct plastic and equipment set up so that bales can be wrapped up as soon as possible to avoid heating.
- You must have bales wrapped up as immediately as possible.
- And not let it go for longer than 12 hours after baling, regardless if you plan on individually-wrapping bales or putting them in a tube.
Silage Livestock Feeds Production:
2. Assess the forage crop
Silage is best made when grass plants are pre-bloom.
Or early flowering (late boot to early head) stage.
Or when legumes are at 10% bloom. Grasses should just start heading out.
- Any perennial forage species or mix can be used for Silage.
- A good hay crop is generally weed-free if maintained as a thick stand.
- But if there are weeds in with crop take note of what they are and their potential issues with livestock.
- Many weeds found in a perennial forage stand are not a danger to livestock when they do not take up the majority of the hay stand. If you only find a few weeds with the crop, and most of it is grass and/or legume mix, then not to worry, as they are very likely to not cause an issue in your animals.
- Perennial forage species that can be used for haylage include (and not limited to) timothy, bermuda grass, alfalfa, red clover, smooth bromegrass, sainfoin, cicer milk vetch, tall fescue, Kentucky bluegrass, orchardgrass, fenugreek, lespedeza, bahiagrass, other fescue and brome grasses, and many others.
- A good rule of thumb to know is that the younger the plant, the higher the nutrient content.
- Most domesticated forage crops should be at least 8 inches tall before being cut or even grazed.
See also: 17 Tips to Start Yam Wholesales Business in Nigeria
Silage Livestock Feeds Production:
3. Cut the crop into swaths or windrows.
Any hay mower will work, as long as they will cut in wide swaths.
Conditioners may be necessary if you are planning on harvesting it as low-moisture (40 to 60% moisture) silage described below.
- It may be good to avoid teddering or raking the mowed forage together because it fluffs up the plants into swaths and make them dry out more than you would want for silage.
- Plus, they make the stems and leaves stick out at random intervals, reducing the effectiveness of a tight bale (if you are wanting to bale it up as baled silage).
- However, teddering has its advantages.
- If the forage crop contains too much moisture and you want to put it up at a good moisture content where it’s not going to be too wet, then tedders and/or rakes may be needed.
- If you wish to have the forage cut into swaths, the next best machine to use is a swather or windrower.
- The swaths will be stacked higher and tighter than what a mower will make, making the process of gathering the swaths, especially if the crop is thick, a slow-moving process.
See also: 20 Tips to Start Rice Wholesales Market in Nigeria
Silage Livestock Feeds Production
4. Let the swathed or mowed forage wilt for a time before harvesting.
Depending on what type of forage you have.
And how wet you want to harvest it at.
You have the options of letting it wilt for not at all, half a day, or for a full day (24 hours).
- In environments where there is no opportunity to allow forage to wilt or dry down to a 40 to 60% moisture content, direct-cut silage may be the best option.
- Forage cut without any opportunity to wilt will be at 75 to 85% moisture, the highest-moisture silage.
- You can get.
- Wilted silage can be allowed to wilt down for half a day (4 to 6 hours) before harvest. Basically, cut forage in the morning, and harvest in mid-afternoon.
- Wilted hay-silage is typically at least 60 to 70% moisture.
- A common problem can be allowing the crop to wilt down too much, creating forage that is too dry.
- This can cause silage to heat, reducing digestibility for livestock, and cause harvest and storage losses, via leaf loss or spoiling, respectively.
- “Low-moisture” silage or what many would consider “normal silage” regardless the forage harvested is gathered at 40 to 60% moisture; compared with wilted silage.
- This silage type often needs longer to wilt down.
- Depending on weather conditions.
- Most recommend a day (24 hours) to wilt down; if the weather is hot enough, though, only half a day (4 to 6 hours) may be needed to get the forage down to that optimum level.
- Grass tends to “dry down” faster than legumes like alfalfa or clover due to its hollow stems, and lower moisture content. However, because the recommended moisture range has a 20% difference, it’s best to take a chance at harvesting a high-legume stand when it’s at least 40 to 50% moisture to prevent leaf-loss during harvest or spontaneous heating.
- Teddering and/or conditioning, as already mentioned, may be necessary to get low-moisture haylage, but this depends on what cutting equipment was used, and other conditions that may make the crop slower to dry than expected (such as rain, heavy dew, etc.).
- If it happens to rain right after cutting the crop, there’s plenty of argument out there that one rain shower won’t hurt the crop so much as it will slow down the time needed to get the crop as dry as you want it to be. Conditioning and raking/teddering may necessary in this case to speed up the drying process before harvest.
- In the next section below, this particular type of silage is ideal for gathering into bales, as baleage or bale silage.
Read also: 47 Ways For Video Editing Business Tips in Nigeria
Silage Livestock Feeds Production
5.Harvest the crop.
Machinery known as “forage harvesters” that are self-propelled or pulled behind a tractor are needed for gathering and cutting up swaths into chopped silage. Cut length is very important, especially for feeding to cattle. Set the cutter head blades so that they are chopping between 1⁄2 inch (1.3 cm) to 3⁄8 inch (0.95 cm).
- With grass silage (if the forage crop is 90 to 100% grass), you can get away with chopping it at 1⁄4 inch (0.64 cm) instead.
- Forage harvesters do not come with a storage compartment like combine-harvesters do when harvesting annual crops for grain like with corn or wheat. Once the forage is chopped up, it is blown out of a long, tall spout; built similarly to a snow blower machine, except twice as big.
- A tractor with a silage wagon (a wagon with three sides built higher than the fourth), a silage truck with similar sides, or a pull-behind wagon (some farmers may call it a “Jiffy wagon”), must be used to gather silage
- An exchange is made between the wagons and/or trucks so that the person operating the forage harvester doesn’t need to stop and wait every so often.
- Once the first truck is full, the harvester stops briefly so that the truck can pull away and the second one moves into position.
- The first truck returns after dropping its load off to get another load, and so the process repeats.
Silage Livestock Feeds Production
6. Drop off the loads to the silage storage site.
Once the wagons or trucks are full they must travel to the site where the silage feed is going to be stored.
This may be a three-sided concrete bunker called a “silage pit,” or on a hill that promotes good drainage.
The wagons or trucks dump the fresh silage into piles situated close together.
And in a manner that is easy to gather and pack into a silage pile.
- Make sure the loads are placed as close to each other as possible.
- When first starting the pile, the first several loads must be place where the pile is going to be.
- After that they are placed close to the built pile, and dumped in a way that is easy for the person in the “packing unit” to move into a pile; i.e., parallel to the pile, and/or in the same direction the pile will be built up as.
Silage Livestock Feeds Production
7.Pack the pile.
The silage pile must be packed very well.
And should be packed down during and after each harvesting day.
In a large operation where several people are employed.
It would be beneficial to have one (a brave one that is not afraid of heights especially) stay behind to operate another tractor or large loader.
That will continuously gather and pack the pile well.
Tractors with dual wheels are recommended to provide the best packing power possible.
See also: 17 Activity Guide On Starting A Distillery Covers Business
Silage Livestock Feeds Production
- Packing is what helps encourage fermentation activity and discourages spoilage.
- The more the pile is packed down, the less pockets of oxygen there is.
- Oxygen pockets create spoiled feed; aerobic-loving bacteria turn it into a brown to black slimy mess, that often smells like tobacco or burnt caramel.
- In other words, instead of fermenting the feed (which is producing a significant amount of acid as a means to preserve the feed), the presence of oxygen decomposes it into a substance equivalent to manure.
- You don’t want feed that is messy and gross like manure (think cow poop).
- If you don’t like the look, feel and smell of it, neither will your animals!
- Haylage/silage piles must be longer and wider than they are tall. The higher the pile is built up, the wider the edges will need to be. A concrete bunker will control how wide you can make the pile, though you can pack several feet above, but only so much that the sides are not over-flowing.
- A rule of thumb for pile-size is larger at the base than the top; no less than 12 to 15 feet (3.7 to 4.6 m) wide at the top to prevent roll-overs or slippage from machinery; and silage piles should only be 12 to 15 feet tall, mainly for farm safety reasons.
- The best way to tell if you have done a good packing job is if you try to sink your fingers into the pile.
- If you only get in so far as your second knuckles of your first three fingers.
- Then the pile has been packed very well, and has potential for being good feed in the winter with minimal spoilage.
See also: 51 Tips to Start Data Scientist Business
Silage Livestock Feeds Production
8.Cover the pile immediately.
Use the proper plastic recommended for silage and silage piles.
Often recommended and used is polyethylene plastic that may be black on both sides or white on one side and black on the other.
The cheaper stuff is all black, but the better quality is the black and white plastic.
- Use 6 to 10 mil plastic. This can be found at your local farm and ranch supply store.
- The heavier the plastic, the more effective it is at keeping oxygen out of the pile and reducing wastage with spoiling.
- The rolls are very heavy. Use a tractor loader with bucket teeth to carry the plastic to the pit so that you can unroll and unfold it.
- A trick to use is to insert a 6 feet (1.8 m) long, heavy iron bar into the roll (like you would hanging a roll of toilet paper on a toilet-paper holder), and fashion thick wire or heavy chain that hangs on the teeth of the bucket. Hang the bar onto this.
Read also:9 Guides To Starting A Distribution Business
Silage Livestock Feeds Production
9.Silage Important:
White and black plastic must be used so that the white side is facing out.
And the black against the fresh silage in the pit.
The white side reflects sunlight and reduces excess heating from the sun, whereas the black side keeps heat inside.
- Trim off extra plastic and use that to cover the edges and sides that the plastic has not covered.
Silage Livestock Feeds Production
10.Weigh the plastic down.
Use numerous old or recycled tires all over the top part of the pile.
Hay bales can also be used to hold down plastic on the sides if the silage pile is not in a bunker.
- Tires are much more gentler on the plastic because they do not cause punctures.
- Punctures are a serious danger of feed spoilage.
Silage Livestock Feeds Production
11.Repair any holes immediately.
Holes in the plastic can cause massive spoilage problems over time.
Spoilage will not be localized, especially if the holes go from a tiny tear to a big rip, especially if wind is a problem.
Follow the same steps for wilting forage as in step 1 of the Harvesting as Chopped Haylage section above.
Note that there may be some discrepancies with best practices for producing baleage or baled silage based on moisture content; this is all depending on your location.
- Most recommended moisture content to put baleage up at is 40 to 60% moisture, particularly in locations where winter and freezing is common. Bales that are wrapped up at a higher moisture content do not keep their heat for long and will freeze into fermented popsicles that are difficult to handle, feed out, and for livestock to eat.
- Baleage at higher moisture (above 60% moisture) is best for locations where freezing temperatures are less common. Several days of temperatures below -10ºC or lower can freeze high-moisture-wrapped bales to literal popsicles.
See also: 33 Top Domestic House Care Tips
Silage Livestock Feeds Production
12.Gather the swaths into a bale with a baler.
Doing this is no different than what you would do making hay.
However, you should not let them get to full size.
Instead, they should only be made to 2/3 to 3/4 their normal size.
Bale silage bales are much heavier, if made to their full size, than normal hay bales (typically baled at 16 to 18% moisture).
Which can make it more difficult for a loader or tractor with a front-end loader to transport from feed yard to corral.
The reduced size should make them easier to manage, plus wrap up.
- Also, use a baler that is built to make very tight bales with tight centres, hence the name.
- A “hard-core” baler is ideal for this because it can pack the swaths into very tight bales with a tight center better than what are called “soft-core” balers.
Silage Livestock Feeds Production
13.Wrap the bales or put them in a tube as soon as possible.
Once the bales are done.
They must be wrapped or put in a tube no longer than 10 to 12 hours after baling; 5 hours or less is more preferable.
This will prevent them from heating.
Which can cause spoilage and even spontaneous combustion.
Especially if they’re baled at 40% or lower in warm conditions.
Read also: 10 Wholesale Plans For Fridges & Freezers Business
Silage Livestock Feeds Production
- There are actually several options available to do this:
- One, you can have a bale wrapping machine hitched behind your baler so that it catches the bale and wraps it up in plastic. This eliminates extra time and extra labour needed to get another machine out to wrap up bales behind you.
- Two, you have another tractor unit that carries a wrapping unit to go in and wrap the bales after the baler has dropped them off.
- For either method, the machine used spins the bale around–regardless if it’s a round bale or a square bale–and wraps it in plastic to the desired thickness. Recommendations range from 4 to 8 mil; higher values are recommended if you plan on carrying over these bales into spring and summer.
See also: 33 Tips For Organizing Counter-tops & Cabinets /Drawers
Silage Livestock Feeds Production
- Three, gather up the bales after baling and put them through a tubing machine that wraps plastic around each bale, but bale faces are together in a long line. You can make bale tubes that are about 100 feet long. Plastic thickness recommendations range from 4 to 8 or 10 mil.
- Square bales in a tube will need to be put together in a multi-bale system. Put them together so that you are putting them in as much of a square face configuration as possible. You will need to experiment to see what will fit best; the Ontario Agriculture link in the Sources and Citations section below has example pictures of what you can use for wrapping square-bale silage.
- Each bale exposed when the tube is opened up will only last for 1 to 2 weeks before spoiling. The bales further down in the tube will not take nearly as long to spoil as that exposed bale.
Read also: 19 Tips To Start Cooking & Baking Ingredients Business
Silage Livestock Feeds Production
- Stacking is a fourth option to use, and is best for large round or large square bales.
- Large round bales can be stacked in a pyramid formation (two on the ground and one at the top, and square bales should be stacked so they form a square-face configuration, as with wrapping.
- They must be covered immediately to avoid potential loss, and as with silage piles above, the plastic weighed down with tires and other hay bales.
- Use a double layer of 6 mil plastic for this system.
- Small stacks makes covering with plastic easier, and will use up excess oxygen within the plastic–as long as the plastic is sealed well with no holes in it–quickly, creating an anaerobic void within that preserves the bales.
- Stacks, once opened, will begin to deteriorate and develop mold and spoilage issues.
- They must be entirely fed out by 1 week in the summer, 2 weeks in the spring, and 4 weeks in the winter, generally.
Read also: 28 Implementation For Starting A Small Scale Business
Silage Livestock Feeds Production
14.Handle individual bales carefully for storage.
You will need to use a different type of loader that is designed to handle wrapped bales without puncturing them.
Which is one that has smooth edges that hug the bale rather than pokes through it.
Like loader bucket with a grapple-fork, or a bale fork.
- Careful handling may be less important with when they need to be fed out.
- But do note that even using a bale-fork or spear.
- Mistakes can happen and you may puncture another bale you intended to leave intact.
Read also:11 Tips To Write Compelling Press Release Reference
Silage Livestock Feeds Production
15. Allow at least 2 weeks to pass before feeding.
Silage Livestock Feeds Production
16.Take only as much as you need.
Especially with chopped silage, only take so much off the face as you need to feed.
It may take practice to understand how much of the face to scrape down and gather for feeding.
But the mathematics with calculating how much face to remove to feed a certain number of animals per feeding.
Can be done for more accuracy, and to obtain a good pit face for your pile.
Good pit faces reduce excessive spoilage or secondary heating.
- This is just as important with baled silage.
- Remember, you are feeding animals a bale that is (or should be) at least 50% water, and you have so many animals to feed and so many bales to put out.
- Less can be more, because the more bales you put out.
- The more likely they will spoil faster than the animals can eat them. You do not what the latter to happen.
Leave a Reply